When it comes to creating own style, screen prints for T-Shirts is a popular choice. This versatile technique allows you to design and print your own T-shirts with precision and durability.
In this article, we’ll dive into the world of screen prints for T Shirts, discussing different types of inks, the printing process, T-shirts design software, T-shirts heat dress, and T-shirts logo design. Whether you’re a DIY enthusiast or a business owner looking to offer custom shirts, this comprehensive guide will provide you with valuable insights.
Types of Inks for Screen Prints for T Shirts
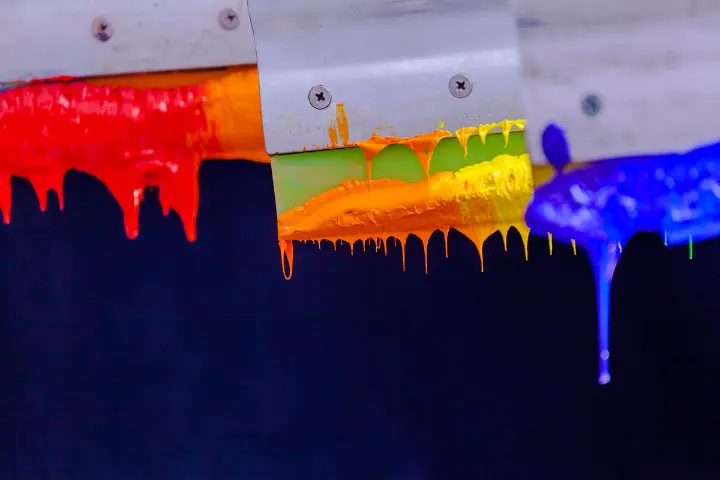
Before we delve into the screen prints for T-Shirts process, let’s explore the various types of inks commonly used in T-shirts printing:
Plastisol Inks
Plastisol inks are a cornerstone of the screen prints for T-Shirts industry, known for their unmatched popularity and versatility. These inks are composed of PVC (polyvinyl chloride) particles suspended in a liquid plasticizer, resulting in a thick and opaque consistency.
What makes plastisol inks so widely used is their ability to produce vibrant, long-lasting prints on a wide range of fabrics. Whether you’re working with light or dark-colored T-shirts, plastisol inks can deliver outstanding results.
They are particularly renowned for their durability, making them a top choice for designs that need to withstand countless wash cycles without fading or cracking. Plastisol inks are also highly customizable, allowing for precise color matching and the creation of intricate designs with fine details.
Despite their many advantages, it’s essential to note that plastisol inks have a distinct feel on the fabric, which can be thicker and less breathable compared to waterbased inks. Nonetheless, their reliability and ability to produce vibrant, opaque prints make them a favorite among screen printers and those seeking high-quality, eye-catching T-shirts designs.
Waterbased Inks
Waterbased inks have emerged as a more environmentally friendly alternative in the world of screen prints for T-Shirts. These inks are formulated with water as their primary base, which significantly reduces their environmental impact compared to traditional plastisol inks.
What sets waterbased inks apart is their ability to provide a soft and breathable feel on the fabric, making them ideal for creating comfortable, everyday wear T-shirts. While they excel on light-colored garments, waterbased inks may not be as vibrant on dark fabrics due to their translucent nature.
They are particularly well-suited for designs aiming for a vintage or distressed look, as they can blend seamlessly with the fabric, resulting in a softer, more muted appearance. Waterbased inks are also known for their sustainability, as they contain fewer harmful chemicals and VOCs (volatile organic compounds), making them a greener choice for eco-conscious printers and consumers.
However, it’s essential to note that working with waterbased inks can be a bit more challenging, as they require specific techniques and equipment for optimal results. Despite these challenges, the eco-friendly and comfortable qualities of waterbased inks make them a valuable option for those looking to produce unique and environmentally conscious T-shirts designs.
Discharge Printing
Discharge printing is a unique and innovative technique within the realm of screen prints for T-Shirts that allows for the creation of vivid and intricate designs on dark-colored fabrics. Unlike traditional screen printing methods that layer ink on top of the fabric, discharge printing involves using a specialized discharge agent to remove or discharge the existing dye from the fabric.
This leaves a blank canvas, ready to be replaced with the desired ink color. The result is a soft, vibrant, and breathable print with minimal ink buildup, offering a distinct look and feel that many find appealing.
Discharge printing is particularly well-suited for T-shirts and garments that require a high level of detail, as it can achieve intricate and precise designs without compromising on the fabric’s texture.
Additionally, because the discharge agent essentially reverts the fabric back to its natural color, the prints are exceptionally soft to the touch, providing superior comfort for those wearing the garments.
One notable advantage of discharge printing is its ability to produce a variety of colors and shades, making it a versatile choice for creating visually stunning designs on dark fabrics. The process does require some expertise, as the discharge agent’s interaction with different dyes and fabric types can vary, but skilled screen prints for T-Shirts can achieve remarkable results.
Whether you’re looking to create custom, high-quality T-shirts with intricate designs or unique, soft-feel prints on dark garments, discharge printing offers an exciting and creative option that continues to gain popularity in the world of textile customization.
The T-Shirts Screen Prints for T-Shirts Process
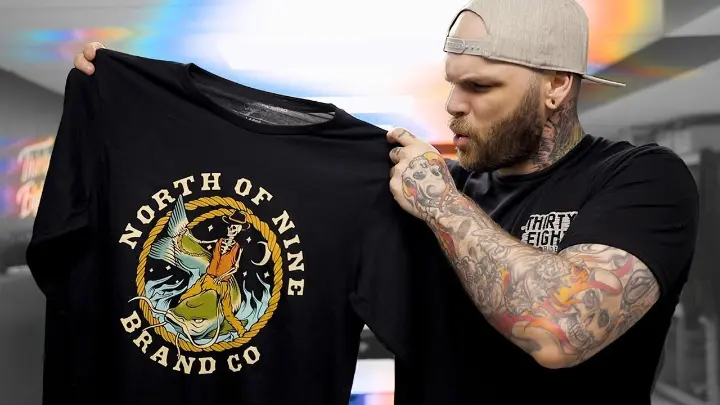
Now that we’ve discussed the types of inks, let’s go through the screen printing process:
Step 1: T-Shirts Design
T-Shirts Design is a crucial and foundational stage in the screen prints for T-Shirts process, where creativity takes center stage. Before you can bring your vision to life on T-shirts, you need to have a well-thought-out design. This is where T-shirts design software becomes your best friend.
With a plethora of powerful tools and features at your disposal, such as Adobe Illustrator, CorelDRAW, or even online design platforms, you can unleash your creativity and craft a design that perfectly encapsulates your message or brand identity. It’s essential to create your design in a vector format, as this ensures that your image remains sharp and clear regardless of its size or scaling.
This step also involves selecting the right colors and considering how they will interact with the chosen ink type and fabric color. Whether you’re designing custom T-shirts for personal use or creating a logo for your business, step 1 is the foundation upon which the entire screen prints for T-Shirts process is built, so take your time, experiment, and let your imagination run wild to achieve the desired visual impact on your T-shirts.
Step 2: Screen Preparation
Screen Preparation is a pivotal phase in the screen prints for T-Shirts process, laying the groundwork for transferring your design onto the T-shirt with precision and accuracy. This step involves the careful preparation of a screen for each color in your design.
The screen serves as a stencil through which the ink will pass, ultimately creating your desired pattern or image on the fabric. The process starts with coating the screen with a light-sensitive emulsion, creating a receptive surface for your design.
Once the emulsion is applied evenly, it’s time to expose the screen to your design. This is typically done using a light exposure unit that shines light through a film positive (a black and white version of your design) onto the coated screen.
The emulsion hardens where the light hits, leaving the rest of the emulsion soft and washable. After exposure, the screen prints for T-Shirts is rinsed with water, removing the soft emulsion and leaving behind a stencil that corresponds to your design.
Screen preparation demands precision and attention to detail. Proper exposure times, the right mesh count for your fabric, and the alignment of multiple screens (for multicolor designs) are all crucial factors that influence the quality of your final print.
Mastery of screen preparation is essential for achieving sharp and well-defined images on your T-shirts, making it a fundamental skill in the screen printing process.
Step 3: Printing
Printing is the heart of the screen prints for T-Shirts process, where your meticulously prepared screens and designs come to life on the fabric of your choice. This step involves a careful and controlled application of ink onto the T-shirt using the prepared screens.
To start, position your T-shirt on a flat surface or a printing press, ensuring it’s stretched tight and secure to prevent any wrinkles or misalignment. Next, place the prepared screen over the T-shirt, making sure it lines up with any previous colors or layers if you’re working on a multicolor design.
Once everything is set, it’s time to load the ink onto the screen. Typically, a generous amount of ink is placed at the top of the screen, near the hinge. Using a squeegee, you’ll then pull the ink across the screen, applying firm and even pressure. The squeegee forces the ink through the stencil (created during screen preparation) and onto the fabric below, transferring your design in the process.
Repeat this process for each color in your design, allowing the ink to dry between layers. Precise registration and alignment are crucial to ensure that the different colors in your design line up perfectly, resulting in a cohesive and visually appealing final product.
While screen prints for T-Shirts can be a labor-intensive process, it offers unmatched precision and durability, making it a preferred choice for many custom T-shirt printers and designers.
The quality of your prints depends on your skill in handling the screen, squeegee, and ink, making it essential to practice and refine your technique to achieve consistently excellent results.
Step 4: Curing
Curing is a critical stage in the screen printing process that ensures the longevity and permanence of your printed design on the T-shirt. After the ink has been applied in the previous printing step, it remains in a semi-liquid state, which means it can easily smudge or wash out if not properly cured.
To cure the ink and make it adhere permanently to the fabric, a T-shirt heat press is commonly used. This specialized equipment combines heat and pressure to effectively set the ink into the fibers of the fabric. The specific curing time and temperature may vary depending on the type of ink used, so it’s crucial to follow the manufacturer’s guidelines or consult with experienced screen printers.
The curing process not only ensures that the ink bonds with the fabric but also helps in achieving the desired color vibrancy and durability. Without proper curing, the ink might flake, crack, or fade after a few washes, compromising the quality and longevity of your printed T-shirts.
Quality control is essential during this step. Inspect the cured prints for any imperfections, such as incomplete curing or misalignment. This careful scrutiny ensures that your final product meets the highest standards of quality and durability.
Step 4 is the point at which your T-shirts transition from a printed design to a lasting piece of wearable art. Proper curing is the key to ensuring that your custom T-shirts remain vibrant and intact, even after repeated washes and wear, making it a vital part of the screen prints for T-Shirts process.
Step 5: Quality Control Screen Prints for T-Shirts
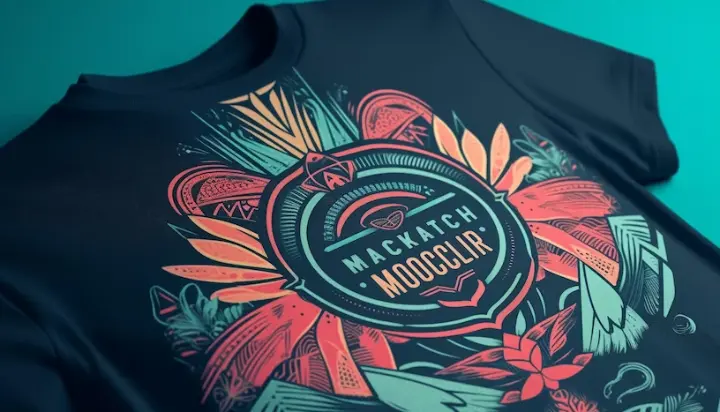
Quality Control is the final and indispensable phase of the screen prints for T-Shirts process, ensuring that your printed T-shirts meet the highest standards of excellence and durability. This step involves a meticulous examination of the finished T-shirts to identify any imperfections, errors, or discrepancies that may have occurred during the printing and curing process.
During quality control, you’ll thoroughly inspect each T-shirt to ensure that the colors are vibrant, the design is clear and sharp, and there are no smudges, misalignments, or defects. It’s essential to pay attention to details, as even the slightest imperfection can affect the overall quality of your product.
This step is especially crucial when you’re dealing with multi-color or intricate designs, as any misregistration or color inconsistency can significantly impact the final appearance.
Beyond the visual inspection, it’s also important to check for proper curing. The ink should be firmly and permanently bonded to the fabric, ensuring that it won’t crack, peel, or fade prematurely after repeated washes. Proper curing is essential for the longevity of your printed T-shirts.
By conducting a thorough quality control check, you can identify and rectify any issues before your T-shirts are made available to customers or used for personal use. This step not only guarantees the satisfaction of your clients but also upholds your reputation as a reliable and professional screen printer or designer.
In the world of screen prints for T-Shirts, quality control is the final seal of approval that ensures your T-shirts are ready to be worn and cherished for years to come.
T-Shirt Logo Design and Customization
With the screen prints for T-Shirts process mastered, you can now focus on T-shirt logo design and customization. Consider the following tips:
- Choose a logo that represents your brand or personal style effectively.
- Experiment with different ink colors and placement options to create unique designs.
- Don’t forget about the type of fabric you’re printing on, as it can impact the final look and feel of your T-shirt.
Conclusion
In conclusion, screen prints for T-Shirts offers a versatile and creative way to customize T-shirts, whether for personal use or as part of a business endeavor. Understanding the different types of inks, including Plastisol, Waterbased, and Discharge printing, allows you to choose the best option for your specific project. So, embrace the art of screen prints for T-Shirts and let your creativity shine on your custom T-shirts!